Sumário
Conceitos Básicos
Gráfico “Dente de Serra”
Variabilidade na Demanda e o Estoque de Segurança
Estoque Médio
Considerações Finais
Download de Arquivos
Você também pode assistir à vídeo-aula a seguir sobre o sistema de revisão contínua para gestão de estoques.
Conceitos Básicos
Sistemas de revisão de estoque exercem dois papéis essenciais no controle de estoques. O primeiro é a determinação de quando novos pedidos de reposição devem ser feitos. Em segundo lugar, os sistemas de revisão definem a quantidade de ressuprimento, geralmente expressa pelo tamanho do pedido de compras.
A principal característica do sistema de revisão contínua é o acompanhamento contínuo dos níveis de estoque. Sempre que retiradas são realizadas, o nível de estoque é prontamente atualizado. Em algumas empresas do setor varejista, isso é feito no próprio ponto de venda, com os níveis de estoque sendo atualizados assim que os produtos são vendidos. Outra característica do sistema de revisão contínua é a existência de um ponto de ressuprimento (PR), que funciona como um gatilho para que novos pedidos de reposição sejam feitos. Assim que o nível de estoque passa a estar abaixo do PR, a empresa sabe que um novo pedido de reposição de tamanho Q precisa ser feito. Em geral, o tamanho do pedido de compra é fixo e é determinado pelo Lote Econômico de Compras (LEC).
Gráfico “Dente de Serra”
Considere o seguinte exemplo: a demanda média de um determinado SKU é 50 unidades por dia e o pedido de compra é de 400 unidades. Quando um pedido é feito, o fornecedor leva 3 dias para realizar a entrega. Além disso, a empresa mantém um estoque de segurança equivalente a 2 dias de consumo. A figura abaixa utiliza uma representação conhecida como gráfico “dente de serra” para ilustrar esse exemplo.
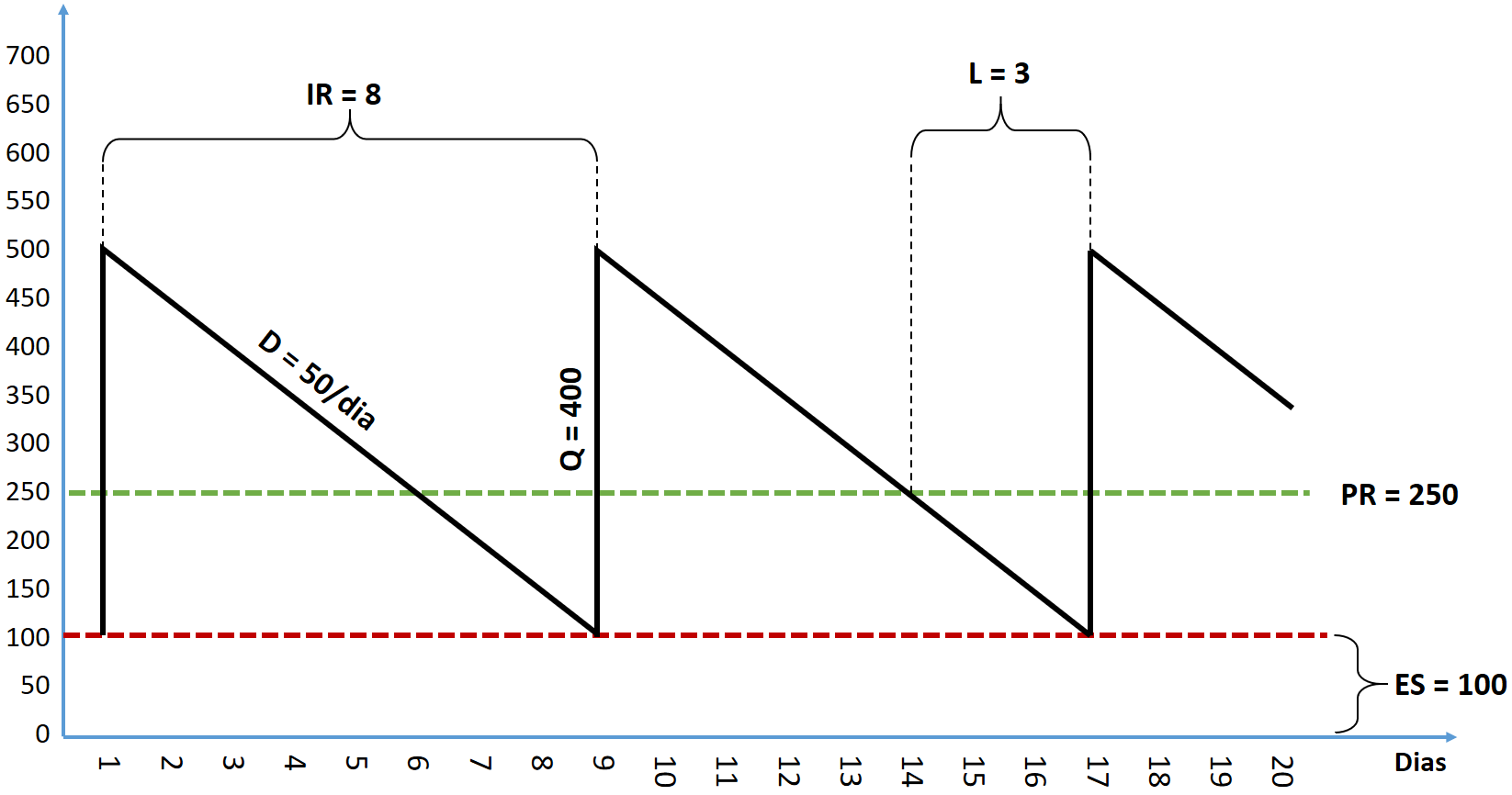
Vamos começar explicando os valores que estão na figura. Primeiro, a demanda (D) é de 50 unidades por dia, o tamanho do pedido de reposição (Q) é de 400 unidades e o lead-time de ressuprimento (L), ou seja, o tempo que o fornecedor leva para entregar o pedido, é de 3 dias.
O intervalo de ressuprimento (IR) é o tempo decorrente entre duas chegadas consecutivas de produtos à empresa. Em nosso exemplo, esse intervalo é de 8 dias. De forma geral, o intervalo de ressuprimento pode ser calculado com a seguinte fórmula:
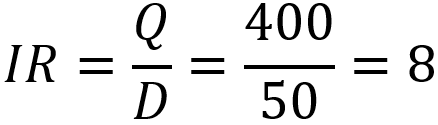
Por fim, o estoque de segurança (ES) é de 100 unidades, pois a empresa mantém o equivalente a 2 dias de consumo para acomodar a variabilidade da demanda enquanto espera pela entrega de novos pedidos. Se você quiser saber mais sobre os métodos de determinação de estoques de segurança, leia este artigo.
No Dia 1, o nível de estoque era de 100 unidades e a empresa recebeu um lote de compra com 400 unidades, elevando o nível de estoque para 500 unidades. Após isso, o estoque foi sendo consumido a uma taxa de 50 unidades por dia. Isso fez com que no dia 6, ou seja, 5 dias após o recebimento do pedido, o ponto de ressuprimento fosse atingido. Nesse momento, um pedido de reposição foi feito ao fornecedor. Ao longo dos 3 dias de espera pela chegada do pedido, mais 150 unidades foram consumidas. No Dia 9, quando o nível de estoque já tinha atingido 100 unidades, o lote de compra finalmente chega, elevando o nível de estoque para 500 unidades e reiniciando o ciclo.
Variabilidade na Demanda e o Estoque de Segurança
Talvez você esteja se perguntando “por que o ponto de reposição é 250 unidades se eu só preciso de 150 unidades durante os 3 dias de espera?”. Outra dúvida comum é “por que preciso de um estoque de segurança se no exemplo anterior ele não foi usado?”.
Para responder essa pergunta, você precisa entender o conceito de variabilidade da demanda. No exemplo, estamos assumindo que a demanda média é de 50 unidades por dia. Esse é apenas um valor médio, o que significa que os valores reais da demanda diária poderão ser maiores ou menores que 50. Suponha que durante os 3 dias de espera pela reposição as demandas reais sejam de 55, 46 e 52 unidades, totalizando 153 unidades. Se o ponto de reposição fosse colocado em 150, teríamos uma falta de 3 unidades, pois não haveria estoque de segurança para absorver essa variação. Usar PR = 150 só seria suficiente se não houvesse nenhuma variação na demanda. Como geralmente temos que enfrentar incertezas na demanda, precisamos manter estoques de segurança para lidar com essas variações e evitar a falta de produtos. Logo, para determinar o ponto de reposição (PR), devemos usar a seguinte fórmula.

A variabilidade da demanda é um dos principais desafios na gestão de estoques. Se mantermos níveis de estoque de segurança muito baixos, a variabilidade fará com que faltem produtos em alguns ciclos de ressuprimento. Para evitar problemas com rupturas de estoque, poderíamos simplesmente manter altos níveis de estoques de segurança. Todavia, essa solução não é economicamente viável, dados os altos custos de manutenção de estoques resultantes dessa abordagem.
Para entendermos como o estoque de segurança evita a ruptura de estoque, considere a demanda da figura a seguir, que cobre um período de 40 dias, com uma demanda média de 50 unidades por dia, com desvio padrão igual a 15.
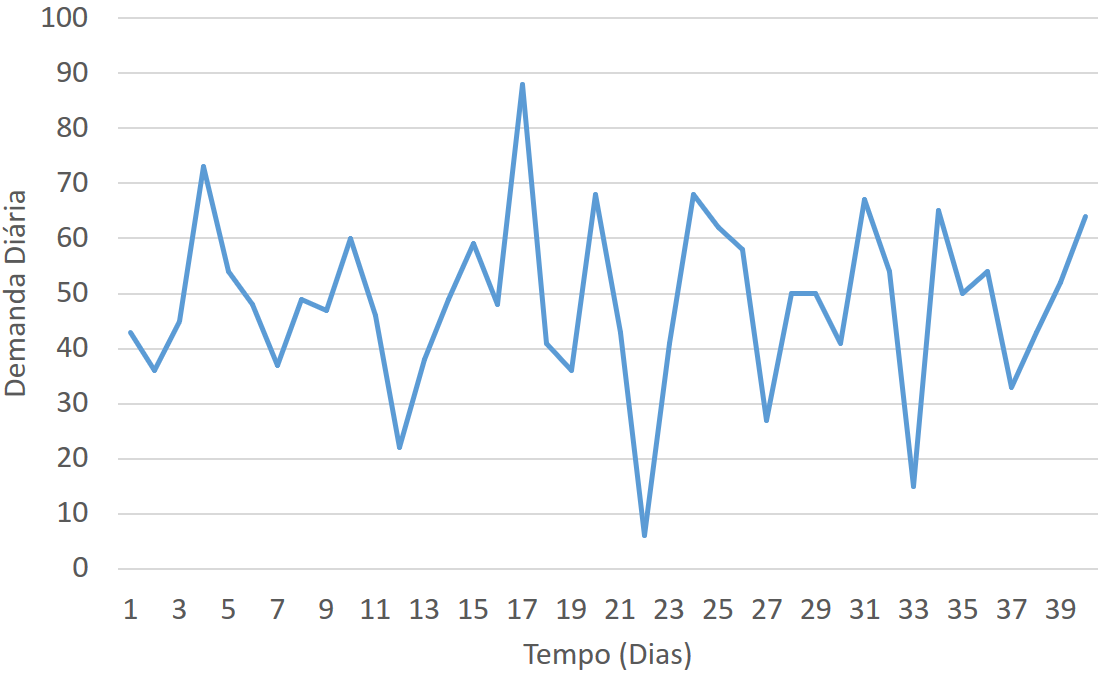
Suponha que o estoque no Dia 1 era de 250 unidades, o que indica a realização de um pedido, que é entregue à empresa 3 dias depois. Se a demanda ocorrer conforme o gráfico acima, os pedidos forem feitos sempre que o estoque no início do período for menor ou igual a 250 e as entregas de pedidos de 400 unidades ocorrerem após 3 dias, os níveis de estoque se comportarão da seguinte maneira (os dados estão disponíveis para download no final da página):
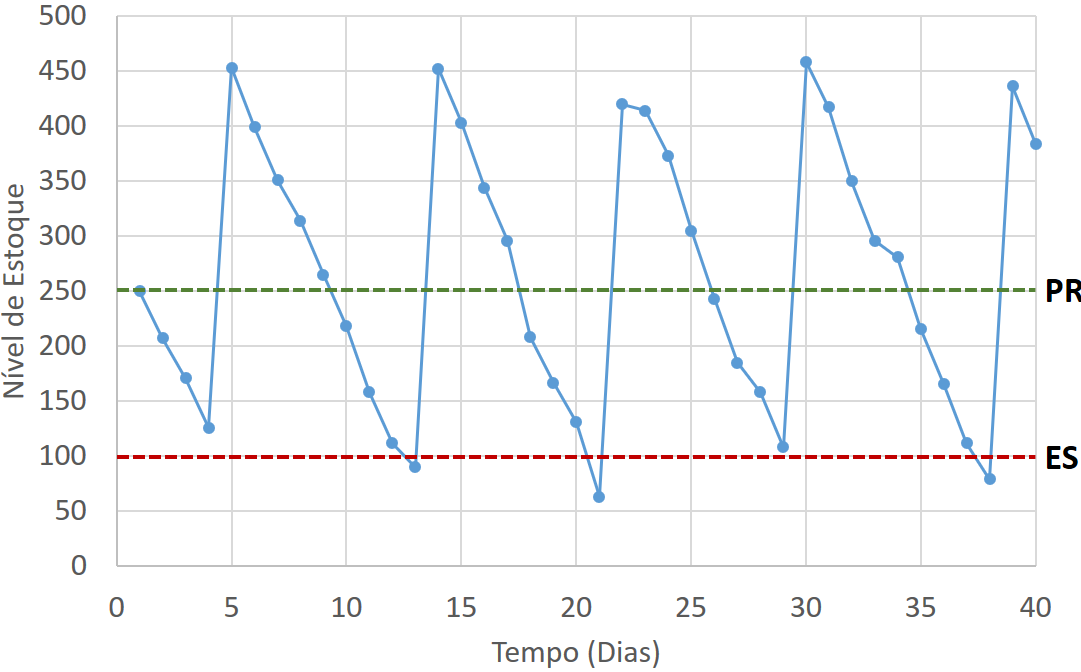
Ao longo dos 40 dias ocorreram 5 pedidos e 5 entregas de lotes de compra. Um ponto importante que deve ser observado na figura acima é que, dos 5 ciclos analisados, em 3 deles o estoque de segurança foi utilizado. Isso significa que se não houvesse estoque de segurança, teria ocorrido a ruptura de estoque, ou seja, não haveria estoque suficiente para atender a demanda até a chegada do pedido de compra. Apesar disso, em todos os ciclos o estoque de segurança foi suficiente para acomodar a variabilidade de demanda e evitar a falta de produtos.
Na verdade, espera-se que em 50% dos ciclos de reposição o estoque de segurança precise ser acionado para evitar faltas de produtos. Um dos maiores segredos é dimensionar o estoque de segurança, de forma que ele seja suficiente para atender à demanda durante a espera pela reposição sem que faltam produtos. Porém, devemos cuidar para não exagerarmos no tamanho do estoque de segurança, pois isso aumentaria os custos de manutenção de estoques.
Estoque Médio
Os níveis de estoque variam a cada dia, tendo um comportamento semelhante ao gráfico “dente de serra” discutido anteriormente. Imagine que queremos saber o nível de estoque médio de um produto. Para fazermos esse valor, poderíamos registrar o nível de estoque ao final de cada dia e calcular uma média desses valores. Isso nos daria o nível médio de estoque ao longo do período analisado.
É possível ter uma boa estimativa do nível médio de estoque de uma maneira bem simples. Seja Q o tamanho do pedido e ES o nível de estoque de segurança, então o estoque médio (EM) é obtido da seguinte forma:
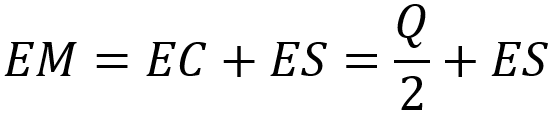
O estoque médio é a soma do estoque cíclico (EC) com o estoque de segurança. O estoque cíclico é o estoque formado devido ao pedido de compra. Se compramos 400 unidades, podemos inferir que isso resultará em um estoque cíclico de 200 unidades. Isso porque, se a demanda for constante, o nível de estoque será 400 no recebimento do pedido, e zero quando o próximo pedido chegar.
O estoque de segurança, por sua vez, é considerado constante ao longo do tempo, pois se a demanda for constante ele nunca será usado. Em nosso exemplo, podemos afirmar que o estoque médio será de:
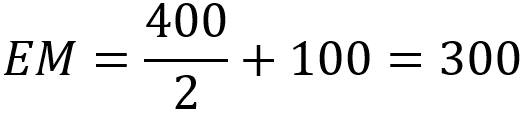
Portanto, em média teremos 300 unidades desse item em estoque. O estoque médio é muito importante, pois é usado para calcular estimativas de custos com manutenção de estoque ao longo do tempo. Também é usado como base para a determinação do lote econômico de compras.
Considerações Finais
Alguns livros de gestão de estoques chamam o sistema de revisão contínua de “sistema de quantidades fixas e intervalos irregulares”. Em situações reais, a demanda é variável e não se sabe ao certo quando o ponto de ressuprimento será atingido. Isso faz com que os intervalos de ressuprimento sejam variáveis. O tamanho do pedido de compra, por outro lado, é fixo e igual a Q. No exemplo que resolvemos anteriormente, veja que o intervalo de ressuprimento entre a primeira e a segunda entregas foi de 8 dias. Já entre a segunda e a terceira entregas, o intervalo foi de 7 dias.
O sistema de revisão contínua tem como principal vantagem a atualização quase que em tempo real dos níveis de estoque, o que facilita a determinação do momento ideal para fazer pedidos de reposição. Este método também facilita o trabalho de contabilidade, pois consegue determinar com mais precisão o valor das mercadorias vendidas ao longo do tempo.
A principal desvantagem deste sistema é a necessidade de implementar sistemas confiáveis para monitorar a evolução dos níveis de estoque, o que pode se demonstrar caro e complexo. Por isso, nem sempre é viável adotar o sistema de revisão contínua para todos os itens. Em alguns casos pode ser mais apropriado empregar o sistema de revisão periódica.